Electrical steel laminations are produced on specialised rapid high-tonnage presses. The type, quality and thickness of materials used to produce the laminations depends on their end use/purpose.
Electrical steel laminations
All laminations are made from high-quality electrical steel of 0.25 to 1 mm in thickness. We offer products in the form of rotor and stator laminations and assembled stator and rotor stacks.
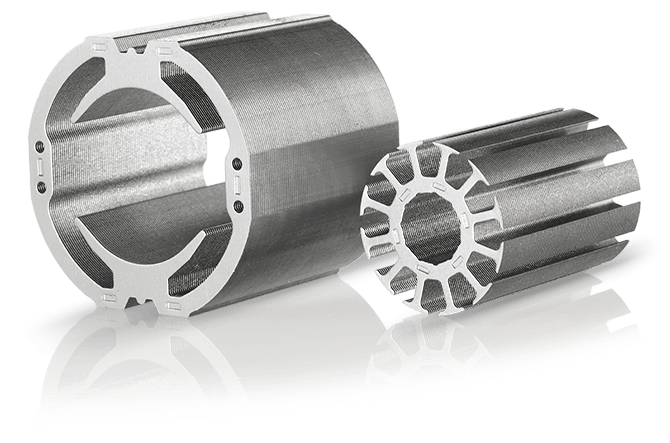
Technologies
Areas of product application
Electrical steel laminations are used in various electric motors that form part of industrial devices where precision, reliability and high efficiency are required. They are used in pumps and motor and pump systems for heating, cooling and air conditioning.
Products
Laminations
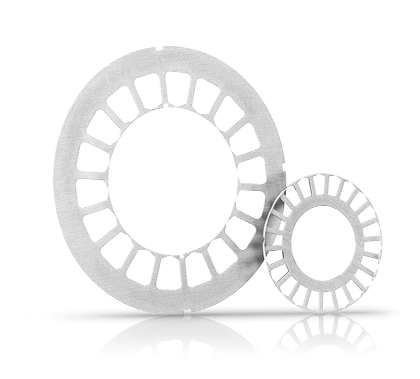
Electrical steel laminations are constituent parts of every electric motor. We produce laminations by stamping electrical steel on high-tonnage rapid stamping presses. To produce the laminations, we need rapid-stamping tools that we design, produce and assemble ourselves. They allow us to achieve the precise geometrical accuracy of final products.
We produce the laminations made of electrical steel for orders of large batches with rapid stamping, in which we use the latest technologies and modern trends in this industry. For some projects, to produce test samples and smaller batches of laminations in the optimal way, we also use the single notching technology or laser cutting.
Areas of product application
Electrical steel laminations are used in various segments of the industry. They are a vital part of automated lines, space and medical technology, industrial motors, pumps, power tools and energy supply, heating, cooling and air conditioning systems.
Stator and rotor stacks
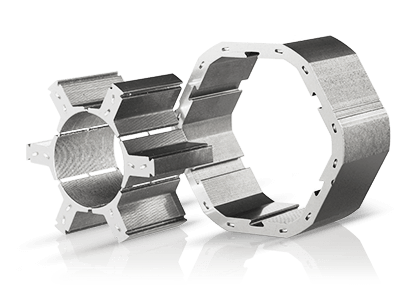
We produce individual laminations and often complete lamination stacks with high-quality, rapid-cutting tools and specialised rapid presses. The process automation that also includes the pressing and measuring devices and product packaging ensures the high reliability, stability and quality of processes.
By means of rapid-stamping tools, we can produce individual laminations or join them into stator and rotor stacks already in the stamping process by means of the technology of interlocking clamps that is integrated into the tool itself.
In addition to the production of laminations and stacks, we offer the annealing process. Processes such as riveting, laser welding or gluing are used to assemble the stacks too.
Areas of product application
Stator and rotor stacks are used in various segments of the industry. They are a vital part of automated lines, space and medical technology, industrial motors, pumps, power tools and energy supply, heating, cooling and air conditioning systems.
Rotors
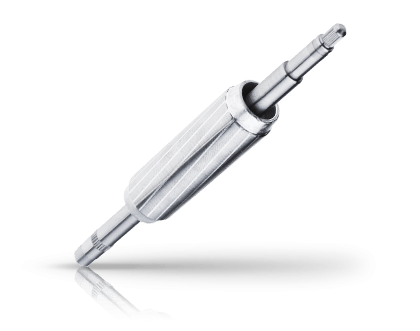
Die-cast rotors form an integral part of high-performance asynchronous electric motors, without which there would be no modern life. We produce them with high-pressure die casting where the rotor stacks are filled with aluminium alloys. In the die-casting process, most attention is paid to the control and quality of the input materials, the repeatability of the process parameters and the temperature control of the moulds. This ensures high-quality die casting and minimal porosity.
We use the technology of high-pressure die casting with aluminium alloys to produce die-cast rotors. Technically pure aluminium with good electrical conductivity is mostly used in this process.
We use the vertical and horizontal rotor die-casting technology allows us to easily adapt to clients’ various requirements and achieve high productivity. We perform other technological processes as well, for example, the embedding of shafts on a rotor and the robotic CNC-machining of rotors and rotors with shafts.
Areas of product application
Die-cast rotors are integrated into industrial motors, pumps, heating, cooling and air conditioning systems, power tools and energy supply systems. They are also vital in automated lines and space and medical technology.